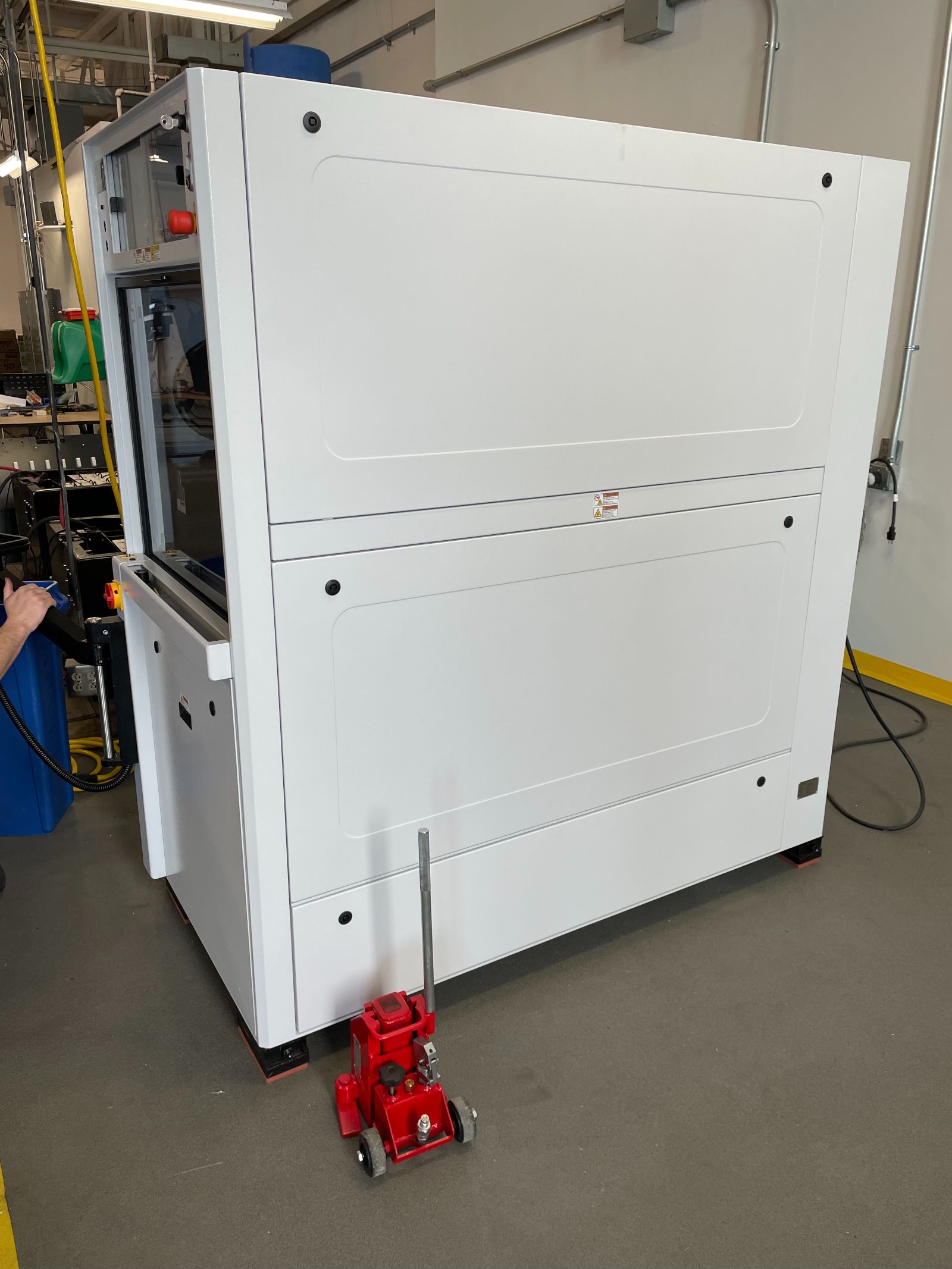
An Industrial Moving Challenge
GKS was approached by technology company Technicity for help moving a large piece of equipment from one building to another.
Technicity is a software development company that provides consulting, design, and deployment support for connected products and Internet of Things (IOT) solutions. Technicity is based in Columbus, Ohio, not far from GKS’s customer support center in Springfield.
Technicity had recently expanded its footprint and was in the process of moving some heavy equipment to their recently acquired spaces. Specifically, the company needed to move a Hesse Mechatronics Bondjet BJ985 from one building to another.
The Bondjet BJ985 is a wire bonding machine, which welds extremely delicate connections at breakneck speeds. These machines must be moved with great care so as not to damage the precision mechanics, but their shape and size can make this challenging. The Bondjet BJ985 measures 53.6 inches wide, 84.4 inches deep, and 75.6 inches tall, and weighs about 3,860 pounds.
Technicity asked GKS for their help moving the machine. With our deep expertise in moving heavy equipment, we knew exactly how to start devising a plan.
Our Strategy for Moving Heavy Equipment
Moving heavy machinery without a plan can end in disaster. From damaged loads to human injury, there can be a high price to pay for poor planning. When we were preparing to help Technicity move their wire bonding machine, we relied on our deep expertise and experience moving heavy equipment to develop an effective strategy.
Understanding the Load and the Route
The first step is to understand both the load and the travel route, especially any challenges or obstacles that might present a problem. This is key to choosing the right industrial lifting and moving equipment.
GKS determined that the weight distribution of the wire bonding machine was close to evenly balanced. We also studied the routes available to us for transporting the load from its current location to its final destination. We identified a few key challenges:
- Uneven flooring transitions. Cracks, doorways, and other irregularities on the travel route can jostle a load if the wrong type of dolly is used.
- Inclines and declines. Managing the weight of heavy loads when traveling up and down ramps or other inclined surfaces can be challenging without proper care.
- Low clearance through doorways. As mentioned, the Bondjet BJ985 is over six feet tall. The average doorway measures six feet, eight inches, which gave us very little margin to work with.
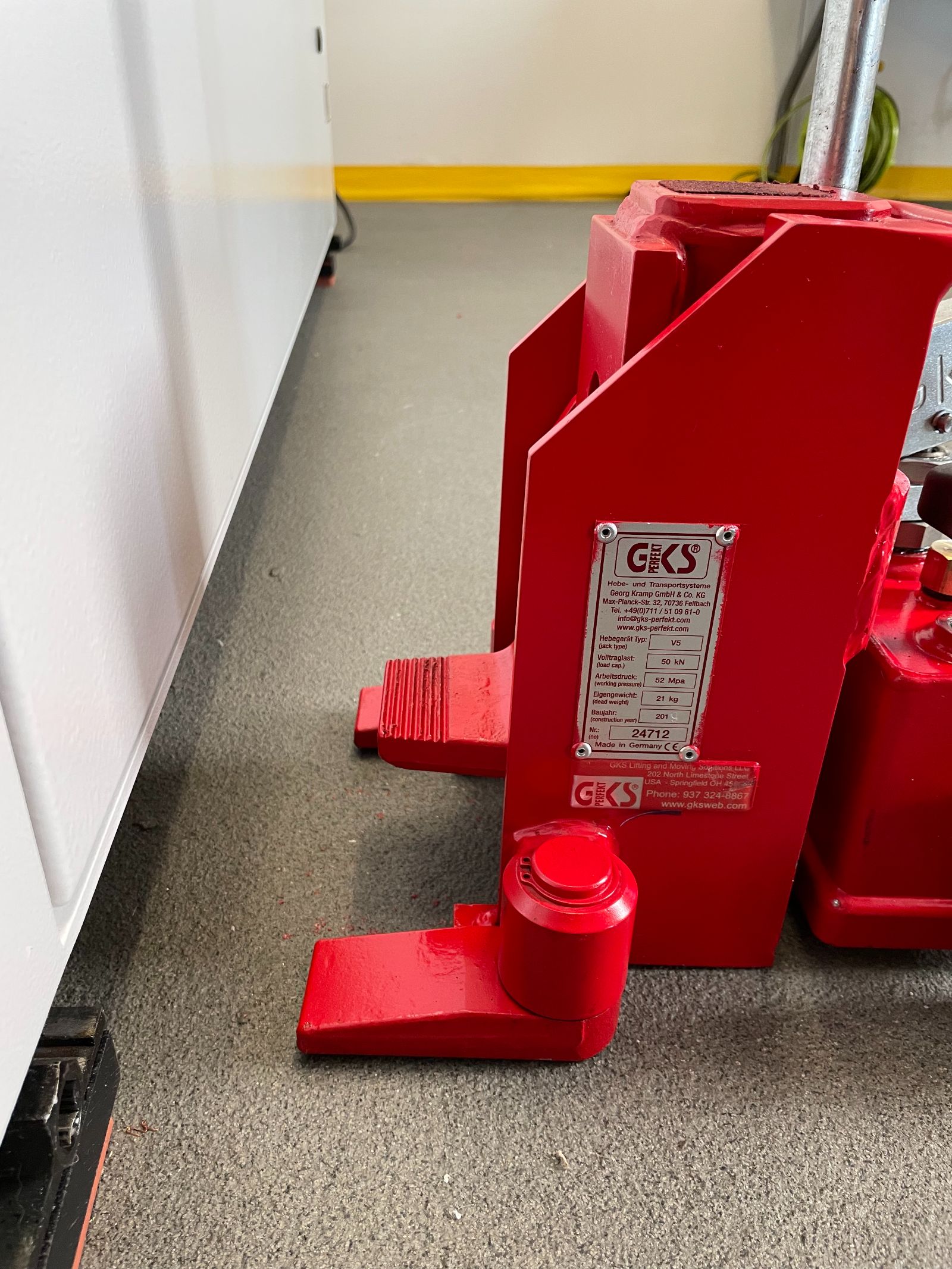
Choosing the Right Moving Machinery
GKS ultimately chose two different types of heavy moving machinery:
- Two V5 hydraulic toe jacks. The GKS V5 hydraulic toe jack has a lifting capacity of up to five tons, or 11,000 pounds, giving us more than enough power to lift Technicity’s wire bonding machine.
A set of F3/L3 dollies. This GKS dolly system is comprised of two separate dollies: An L-dolly, or lead dolly, which has a bar for towing and a swivel plate for steering, and an F-dolly, or following dolly, which consists of two straight-line skates that can be adjusted for width. The carrying capacity of each is three tons, or 6,600 pounds (see note). Together, the two dollies create a three-point system that navigates smoothly overly uneven flooring transitions, which prevents the load from rocking, tipping, or excess jostling. Additionally, the loading height of the F3/L3 dollies is just 4.3 inches, which keeps the load as low to the ground as possible, a critical consideration for low clearance doorways.
Note: Had the weight of the wire bonding machine been unevenly balanced, we would have made a different choice and opted for one skate with increased carrying capacity to accommodate the extra weight.
Lifting and Securing the Load
Once we had chosen the right equipment for the load and the route, we were ready to begin. We placed two of our V5 hydraulic toe jacks at the back of the machine, at opposing corners, to begin the lift. We verified that both jacks started in the same lifting position, with their feet facing forward, for maximum stability. The jack operators counted off in sync to ensure they were lifting the load evenly. (Alternatively, a single operator could have used a GKS PV hand pump to lift both jacks, which would eliminate the need to count off and reduce the number of people needed to execute the lift.)
Once the back end of the machine was lifted high enough, we placed the F3 dolly underneath and slowly lowered the machine down onto it. When using a three-point system, we always recommend starting with the following dolly to ensure the load is as stable as possible when lifting the second side.
After the load was secured to the F3 dolly, we moved the two V5 jacks to the front of the machine and repeated the process with the L3 dolly. It’s important to center both dollies as best as possible, to ensure maximum stability.
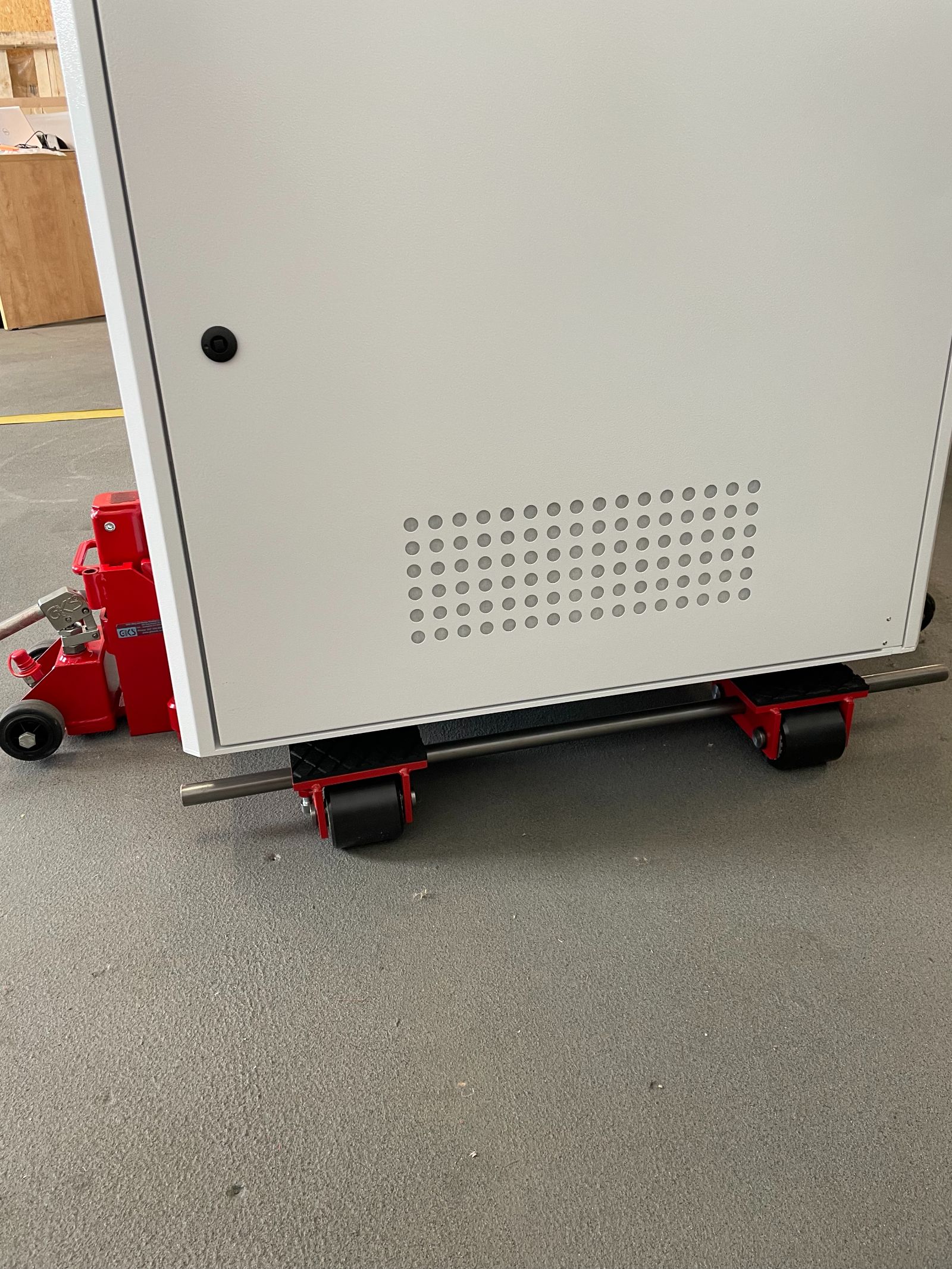
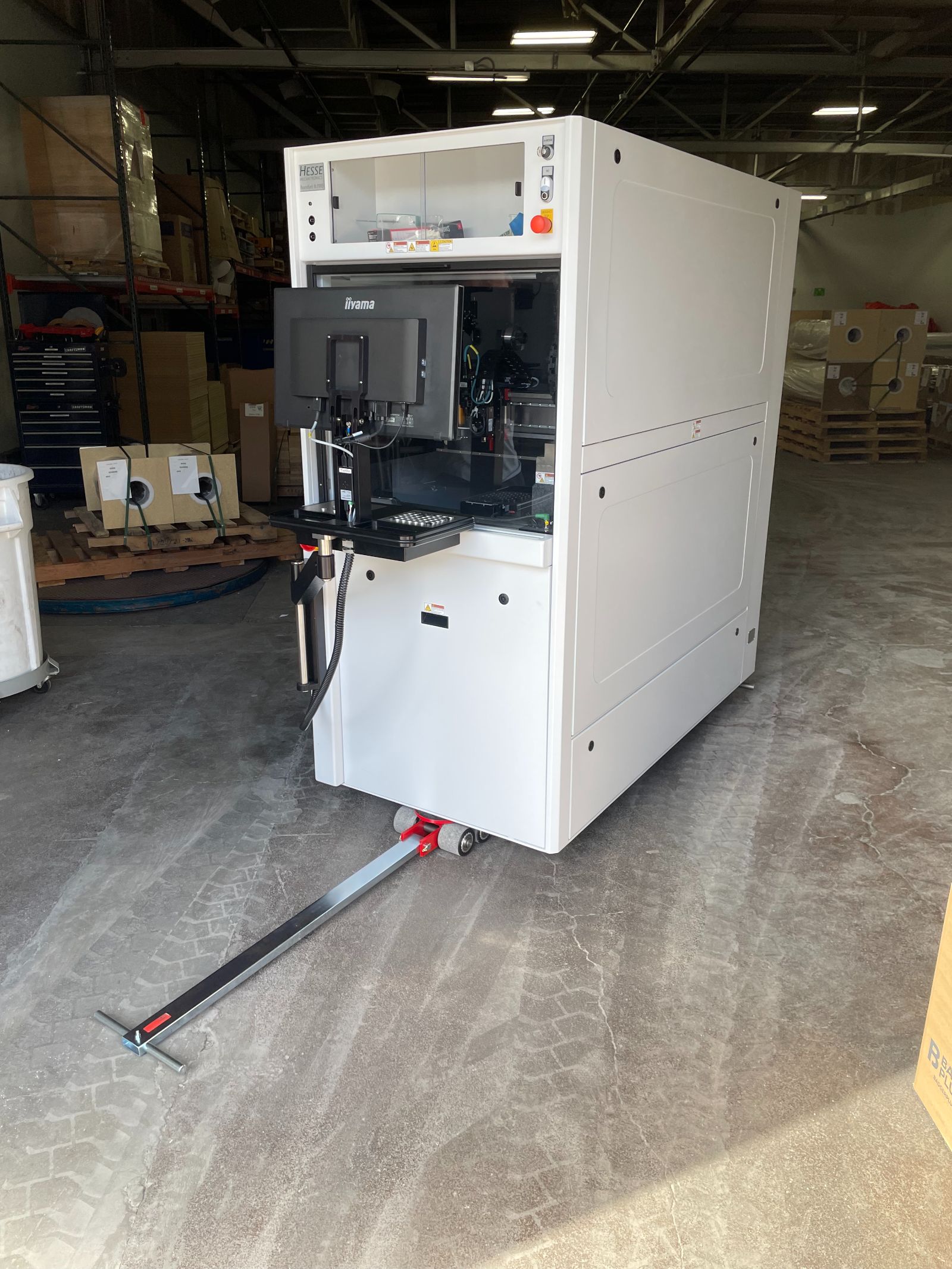
Moving the Load
Once the wire bonding machine was securely loaded onto the F3/L3 industrial skates, we could pull and guide the load through Technicity’s facility with minimal effort. As previously mentioned, the 4.3-inch loading height of the dollies allowed us to travel through doorways with plenty of clearance.
Once we exited the facility, we had to guide the load down a ramp and across the road to another Technicity building, its new home. Thanks to the three-point loading system created by the F3/L3 dollies, we were able to navigate across uneven pavement, cracks, and other obstacles without issue, protecting the wire bonding machine’s delicate inner workings from getting bumped around too much.
The three-point loading system also allowed for precise maneuverability and ninety-degree turns when we entered the new building. We traveled around a few tight corners before placing the load to exactly where Technicity wanted it.
Deloading Heavy Equipment
The final step after determining load placement was to reverse the loading process. We removed the L3 dolly first, followed by the F3 skates, and the move was complete. The wire bonding machine was undamaged, and Technicity didn’t have to worry about adjusting its placement.
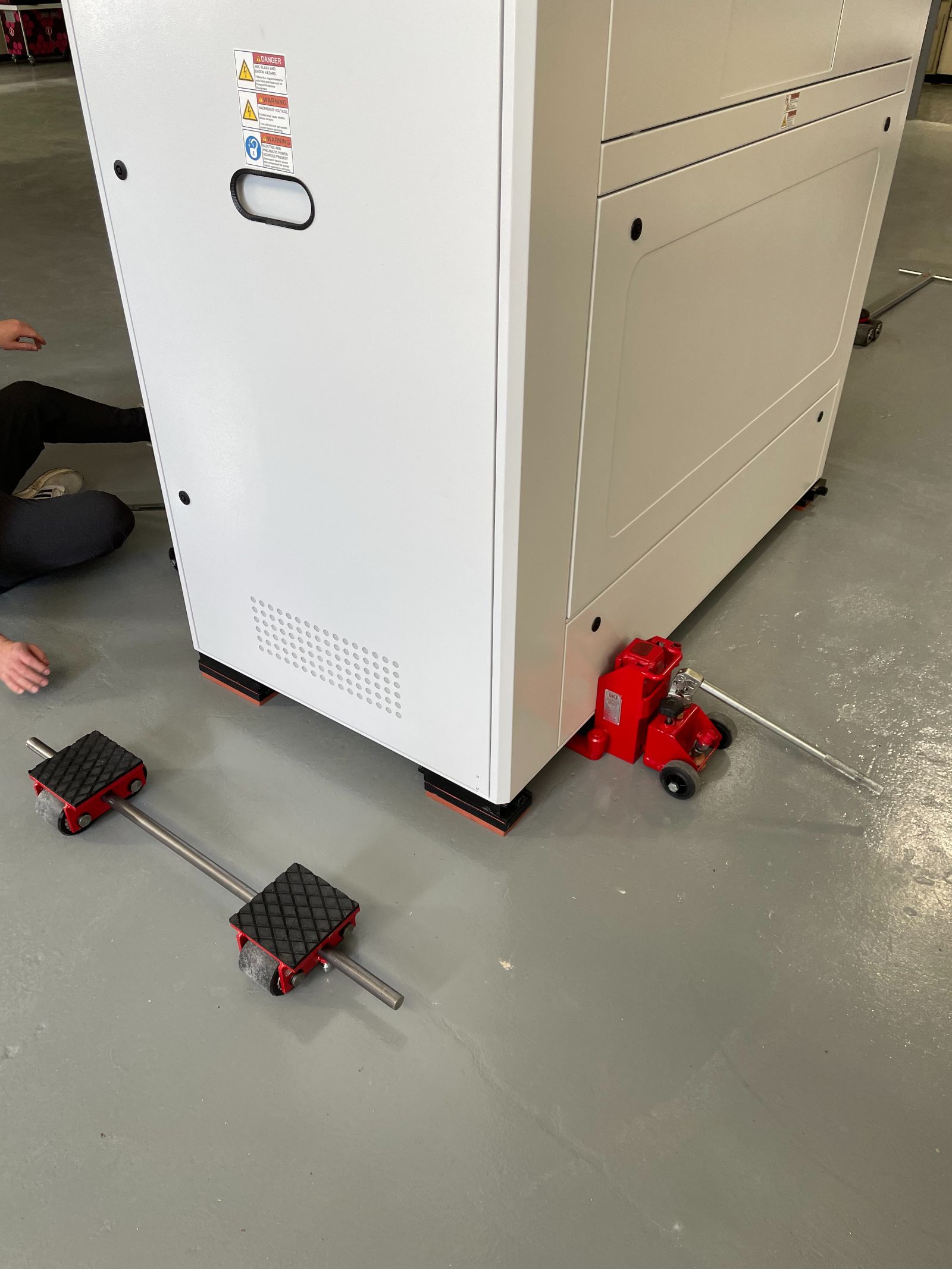
Why Our Heavy Equipment Moving Strategy Worked
There are a few key reasons why we were able to successfully move a heavy piece of delicate equipment across uneven flooring transitions and pavement without issue.
- We thought about the move holistically. We assessed every risk factor, every obstacle along the travel route, and the size and weight of the load, and we chose our equipment accordingly. By considering every element of the move before making any decisions, we saved ourselves from frustration and protected Technicity’s investment from damage.
- We used our own products. There are many ways to move heavy loads, but it’s tough to beat GKS moving equipment. GKS dollies deliver unmatched stability, low loading height, and tight turning radius, all factors that proved invaluable during this move.
Industrial Moving Equipment From GKS
GKS has leveraged the best of German engineering to make a line of top-quality moving equipment for every heavy-duty moving scenario. GKS transport dollies provide stability and precise maneuverability, with a carrying capacity up to 60 tons. Our hydraulic jacks can lift up to 30 tons, and many can be operated via external hydraulics to reduce labor. Our customer support team, located in the American heartland, is available around the clock to advise on the best equipment and strategy for even the most complex moving challenges. We can help you choose the right equipment for your needs, so you can maximize your investment—and protect it with our five-year warranty on every product.
To learn more about GKS moving equipment or discuss a moving challenge, talk to a member of our team >